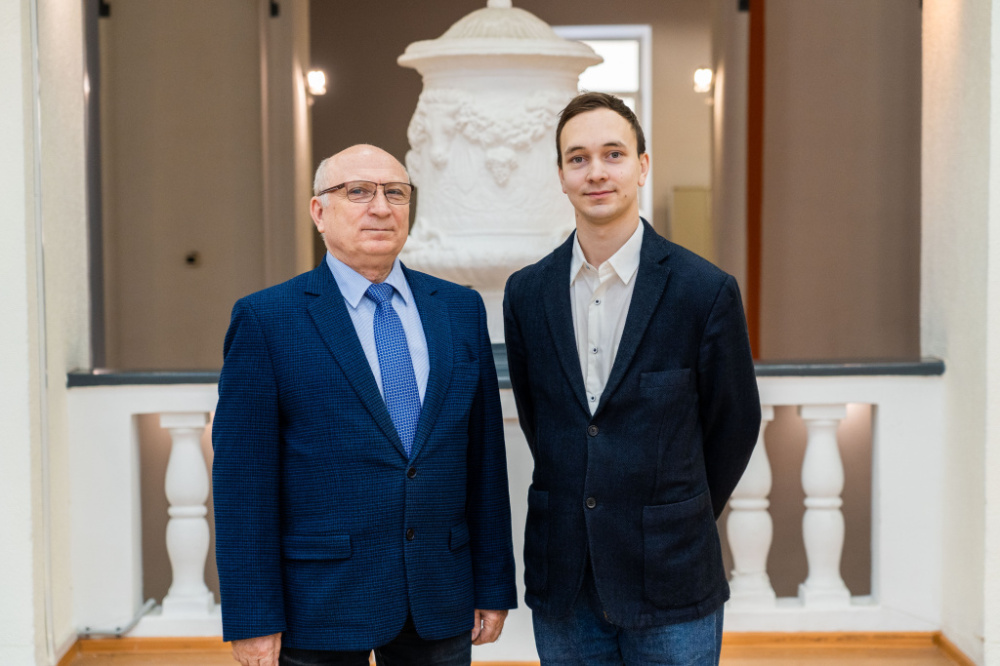
SPbGASU has developed a forklift hydraulic schematic with a slewing mechanism. Received a patent for invention No. 2783756.
The team of authors included members of the Department of Land Transport and Technological Machines PhD student Dmitry Semenov and Professor Ivan Vorontsov. We asked the young researcher to talk about his work.
– I got interested in the hydraulic schematic of lifting and transport, construction and road machines in the third year of the SPbGASU Faculty of Automobile and Road Building, where I studied in the direction 23.05.01 “Land transport and technological means”.
I faced the question where to start. The first steps in improving the hydraulic schemes and working equipment of machines were made on the basis of an earth-moving machine - a scraper. Together with professor at the Department of LTTM Sergey Vasilyevich Repin and senior lecturer at the Department of Transport Systems Aleksandr Aleksandrovich Belekhov, we made a detailed design calculation of the system, taking into account additional elements. Later, the hydraulic scheme of the scraper was presented for defense in my final qualification work, and the methodology for designing the hydraulic system itself became the basis for further study.
I became interested in warehouse equipment, in particular, in a forklift loader, at the beginning of my PhD studies. At that time, I often visited warehouses, where I observed production processes, communicated with personnel, studied the principle of operation of a forklift. Then, using information fr om foreign publications, I conducted a comparative analysis of warehouses located in Europe and Asia. As a result, I became interested in how the forklift could be upgraded so that the productivity of warehouse work increased, and the machine of domestic production could compete with foreign counterparts. And for the past three years, my scientific work on upgrading the forklift has continued.
The idea of the study was supported by my supervisor, professor at the Department of LTTM Ivan Ivanovich Vorontsov. The forklift hydraulic schematic is part of a dissertation that is directly related to a digital model of an unmanned forklift. Together with the supervisor, technical solutions for the modernization of the machine were discussed, calculations were made for the hydraulic system and the slewing mechanism, and the research was tested at conferences and in scientific journals. I am also grateful to Ekaterina Aleksandrovna Laushkina, specialist of the Division for Scientific Work, for her help in preparing the scientific development in accordance with the requirements of the Federal Institute of Industrial Property.
General view of a forklift with a slewing mechanism: 1 – mast, 2 – carriage, 3 – lifting forks, 4 – worm gear, 5 – hydraulic motor, 6 – operator's cabin, 7 – counterweight, 8 – wheeled machines
Forklift with a slewing mechanism, top view: 1 – lifting forks, 2 – carriage, 3 – mast, 4 – slewing mechanism, 5 – counterweight
– Has anyone worked on this before?
– They started discussing the improvement of forklift in the middle of the twentieth century, when most European and Asian manufacturers decided to test the machines on electric power plants, while reducing the size of the machine itself. Currently, there are two types of forklift working body arrangement - side and straight. Depending on this arrangement, over time, varieties of loaders appeared - stackers and reach trucks.
The point of the loader slewing mechanism was first announced and described in the UK by engineer Frederick Leslie. Later, another engineer, Robert Dundol, tried to offer a slewing mechanism in a forklift. But they did not offer an appropriate hydraulic scheme for the operation of the machine, but focused only on the design of the new unit. Development of advanced hydraulic schemes for forklifts is rare these days, since the direction in question is unified and is popular only in situations wh ere a problem arises that cannot be solved with a basic machine.
– Why upgrade loaders?
– The relevance of the issue is due to the size of the warehouse: the forklift needs to make several maneuvers to turn 90 degrees to the warehouse shelf and unload the pallet with cargo, and these facilities are not always spacious. We proposed to use a modification of the working unit, equipping it with a slewing mechanism, and the hydraulic scheme with a hydraulic motor that would control the operation of the unit. At the same time, the adjustment of the supply of the working fluid in the system must be made not stepwise, but volumetrically stepless, which will allow lifting / lowering the load-gripping forks and turning the working unit smoothly, excluding sudden movements and shocks.
The hydraulic schematic and associated slewing mechanism can be used in warehouses with aisle widths not exceeding 1.75 meters. The development may be of interest to organizations involved in the storage and sorting of food industry products, logistics companies for the delivery of household appliances and tools, enterprises in the field of mechanical engineering and machine tool building.
– How did your work go?
– Research work began with a problem statement. We interviewed the workers of the logistics company. During the interviews, they revealed the low productivity of warehouses and came to the conclusion that it is necessary to improve the existing forklifts. At the same time, the modernization method must have been universal and applicable to any model of the machine. The second stage included the study of existing forklift solutions. Among other things, we considered modern technologies - virtual and augmented reality, automated warehouses, unmanned forklifts. Based on the results of the search, it was decided to improve the forklift with a slewing mechanism and modernize the hydraulic scheme. Then the calculation phase began. Based on the methodology for designing the hydraulic scheme of the scraper, the calculation of the forklift scheme was carried out, taking into account the addition of a new device to the system - a hydraulic motor. The obtained theoretical results showed that the system will withstand the required load, and the slewing mechanism will properly perform its function. After that, the performance of the rotary unit, taking into account the operation of the hydraulic system, was tested using computer simulation - the result was positive. The final stage in the development of the upgraded forklift hydraulic schematic was the filing of an application for an invention.
– What are your further plans?
– In the future, I need to include a description of the slewing mechanism in the content of my PhD thesis, automate the forklift by writing a computer program, and create a digital model of the duty cycle control system. Then it is necessary to embody the result in the form of a prototype and defend this study in the PhD thesis. In the future, I plan to start upgrading other hydraulic systems of lifting and transport, construction and road machines, since domestic equipment must comply with modern development trends and compete with European and Asian counterparts.
.jpg)
.jpg)
- Forklift hydraulic schematic with a slewing mechanism: H1 and H2 - hydraulic pumps, P1 - distributor block, C1 and C2 - mast position control cylinders, C3 and C4 - lifting cylinders for lifting forks, C5 - changing the position of the carriage, C6 - steering cylinder, M1 - hydraulic motor control of the slewing mechanism
- Forklift slewing mechanism: 1 - mechanism support shaft, 2, 4 - guide rods, 3 - support bearings, 5 - worm gear of the slewing mechanism, 6 - hydraulic motor